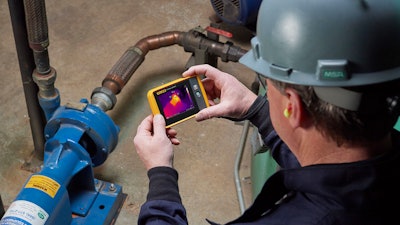
In the modern industrial landscape, safely maintaining and operating equipment is critical in sectors like manufacturing, engineering, automation and maintenance. Preventive maintenance, where professionals check, troubleshoot and replace worn parts before they fail, is key to avoiding unexpected downtime.
Catching problems early requires detecting signs of wear before a machine breaks down. One major indicator that equipment may be in the early stages of failure is when it begins to overheat.
The right tool is necessary to detect overheating. One technology that has revolutionized industrial maintenance is thermal imaging. Thermal imagers have proven to be game-changers in detecting and diagnosing issues in industrial machinery and helping technicians stop machine damage before it becomes costly and dangerous.
How Thermal Imaging Minimizes Heat Damage
Overheating machinery is associated with a number of risks on the factory floor. It is a common cause of industrial accidents and can cause extensive damage to equipment when left unchecked.
By identifying overheating parts or those at risk of overheating, technicians can take the necessary precautions to ensure the safety of their staff and minimize further damage to equipment. This is where thermal imaging comes in.
Thermal imagers use a method of capturing images of an object by detecting the infrared radiation it emits. It allows for non-contact visual identification of hotspots which can be indicative of potential faults or failures. By identifying potential problems early, thermal imaging helps industries avoid costly repairs or replacements. It also reduces the time spent on routine inspections, hence increasing operational efficiency.
Thermal imaging has given a significant boost to predictive maintenance practiced across a variety of industries. This technology helps identify anomalies before they escalate into significant problems, thus facilitating timely intervention and reducing downtime.
Fluke
Thermal Imaging Applications
Before a piece of equipment overheats, there are often anomalies that can be detected with thermal imagers. Detecting problems early, before they escalate into significant problems, facilitates timely intervention and reduces downtime.
Here are a few scenarios where thermal imaging can help spot issues early:
- Electrical systems - Thermal imaging can detect overloaded circuits, loose connections and other electrical issues that could lead to equipment failure or fire hazards.
- Mechanical equipment - This technology can identify excessive friction in moving parts, which could be a sign of wear and tear. It can also detect misalignment in mechanical parts, facilitating timely repairs.
- HVAC systems - In heating, ventilation and air conditioning systems, thermal imaging can detect blockages, leaks and insulation problems, ensuring optimal performance.
Selecting the Right Thermal Imager
Many different thermal imagers are sold today. Consider the following when choosing the right thermal imager:
- Application - What you're planning to use the thermal imager for will largely dictate which one you should choose. For example, an indoor electrical panel inspection taken from a close distance versus an outdoor transformer inspection from a long distance would have differing primary needs.
- Resolution - This is the number of pixels in each image. In general, more pixels provide a more detailed and clear image.
- Sensitivity - This refers to the smallest temperature difference the camera can detect. For most applications, a sensitivity of 0.1°C is adequate, but for some tasks (like detecting moisture in walls), better sensitivity might be needed.
- Temperature range - Thermal imagers are specified by the range of object temperature they can detect. Be sure to choose a thermal imager that meets your needs.
- Ease of Use - Some thermal imagers are more user-friendly than others, with intuitive interfaces and easy-to-navigate menus. Focus capability can make or break the ease of inspection. A large color LCD screen aids in visualization while on site.
- Durability - If you expect to be in dirty environments or want more assurance the imager will hold up to bumps and drops, then consider the ruggedness of the imager.
- Software - Some thermal imagers come with software that can generate detailed reports from the thermal images, which can be very useful for documenting and analyzing your findings.
- Price - Finally, the cost can be a deciding factor. Higher-end models with more features and better performance will obviously cost more, but there are plenty of affordable options that still offer good quality. Consider what is most important to you in your application.
No matter which thermal imager you choose, effective use of thermal imaging technology requires thorough training and expertise. Professionals should be adept not only at operating the devices but also at interpreting the data they provide. Comprehensive training programs should cover these aspects, ensuring that thermal imaging is utilized to its full potential to enhance safety and efficiency.
Fluke
The Future of Thermal Imaging in Industrial Safety
In the modern plant, thermal imaging will continue to be an integral part of industrial safety protocols. Future devices may offer greater accuracy, improved resolution and advanced analytical capabilities. However, the core goal will remain the same: detect equipment overheating early to ensure operational safety and efficiency.
Recognizing and addressing temperature issues is fundamental to enhancing the longevity and reliability of industrial systems, ensuring they operate smoothly and safely in a demanding industrial environment.